A Marquise Masterpiece
An incredible 2.33ct Marquise Diamond was brought into us by our client as they wanted to have it remounted and updated. The original ring mount was originally made for the client in the 90s by a well known West End Jeweller - the design was of its time and our client was after a change!
The D Colour, internally flawless diamond was removed from the old ring mount and carefully measured and photographed, in order that we could create the new ring mount in our CAD software (3design and zBrush) around the stone and build the individual components that form each part of the ring - the centre collet, the collets for the diamonds on the shoulders and also the pilot holes for the round diamonds which have been grain set into the shoulders.
After hours of careful work, we were happy with the design work (created by my father Tim Roe) we put forward the design to the client for approval. When approved we then submitted the STL file to our casting partner in the Jewellery Quarter in Birmingham.
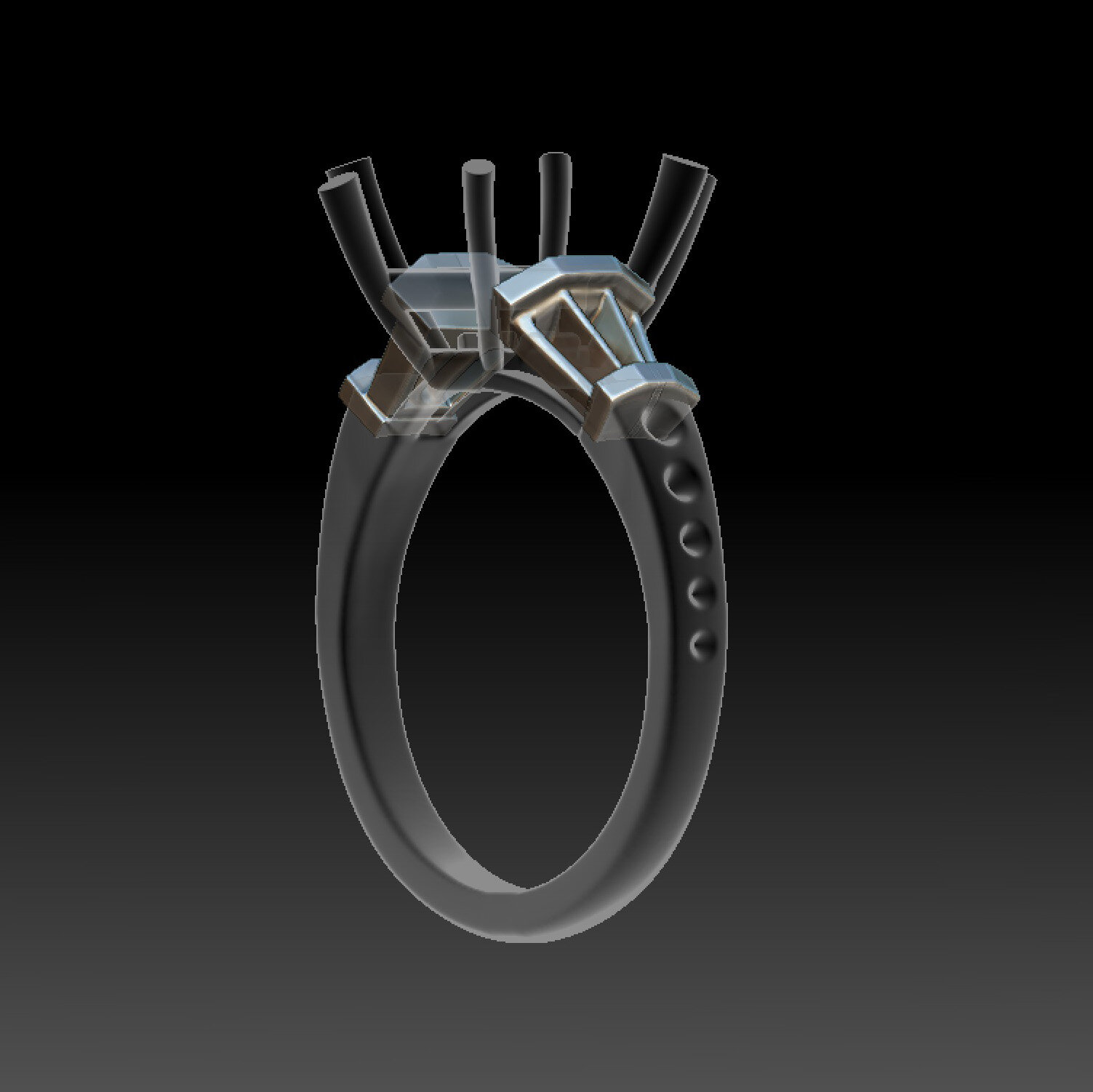
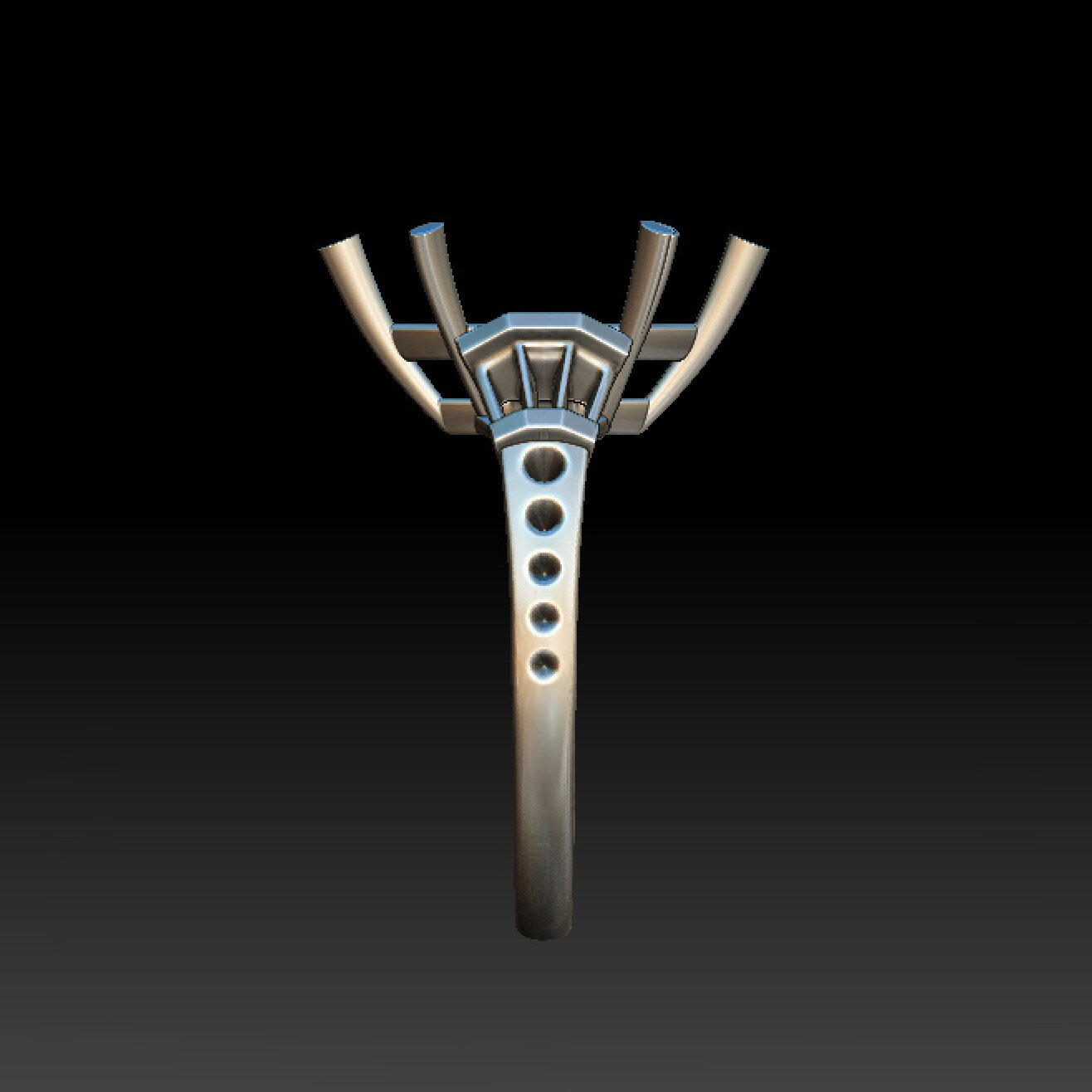
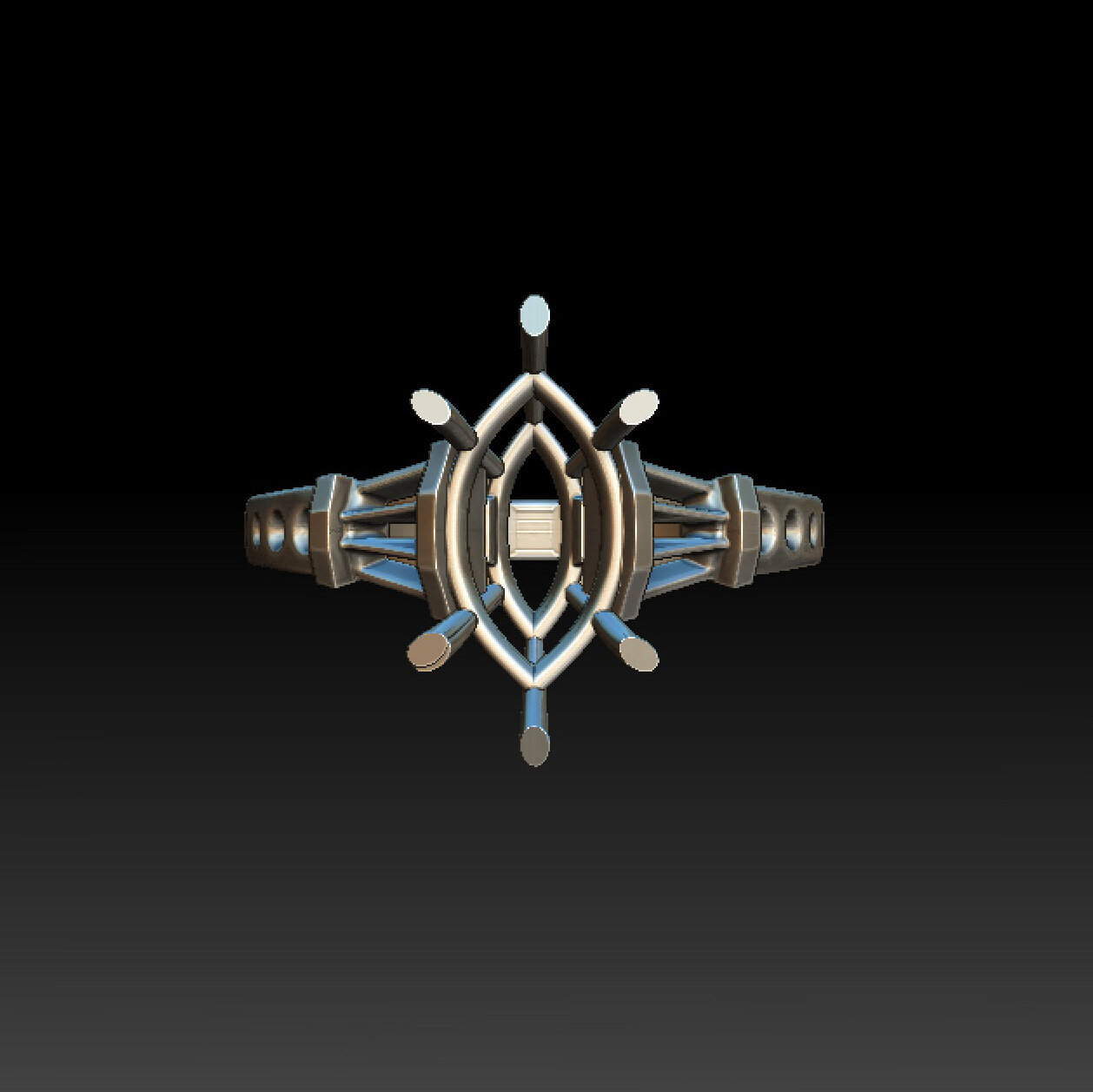
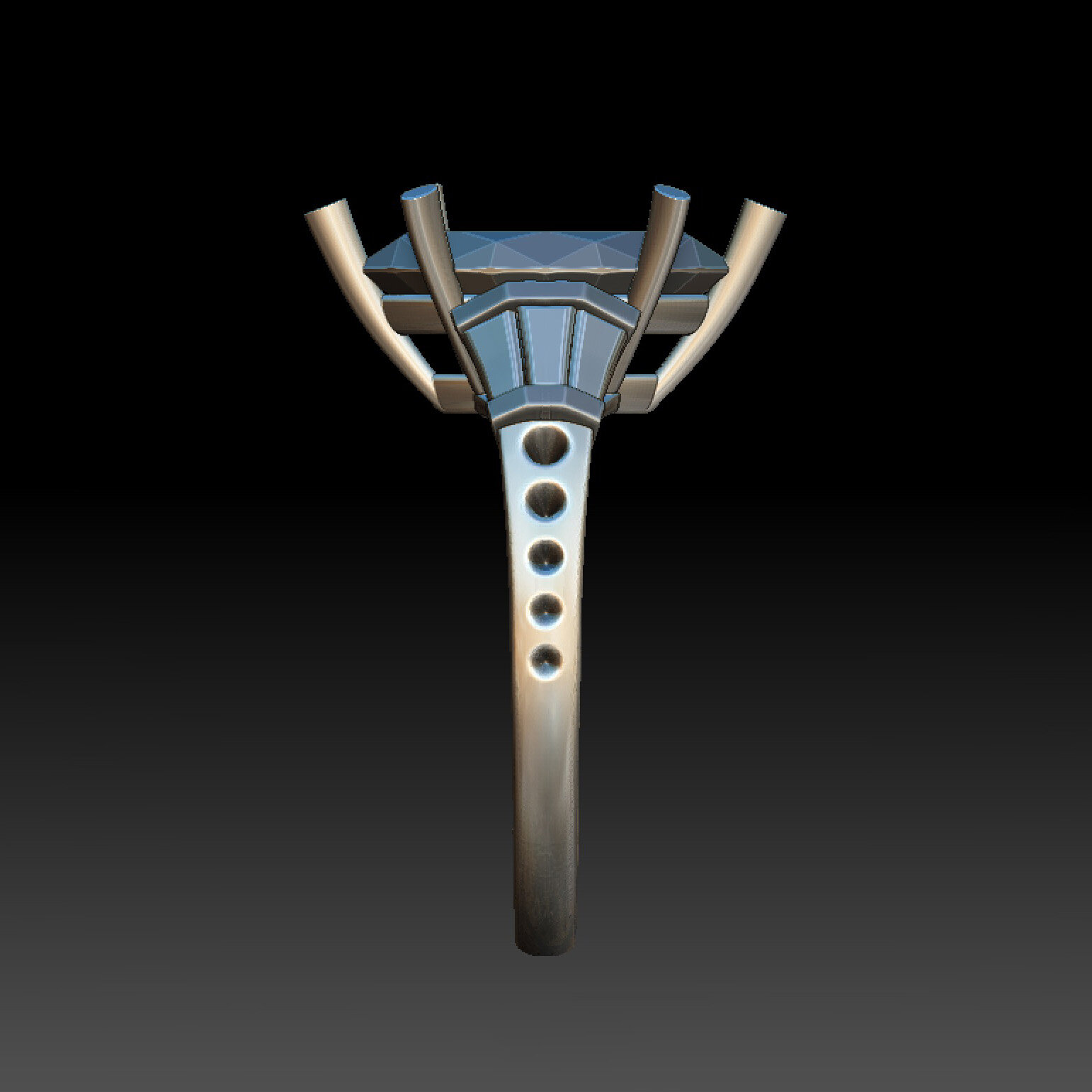
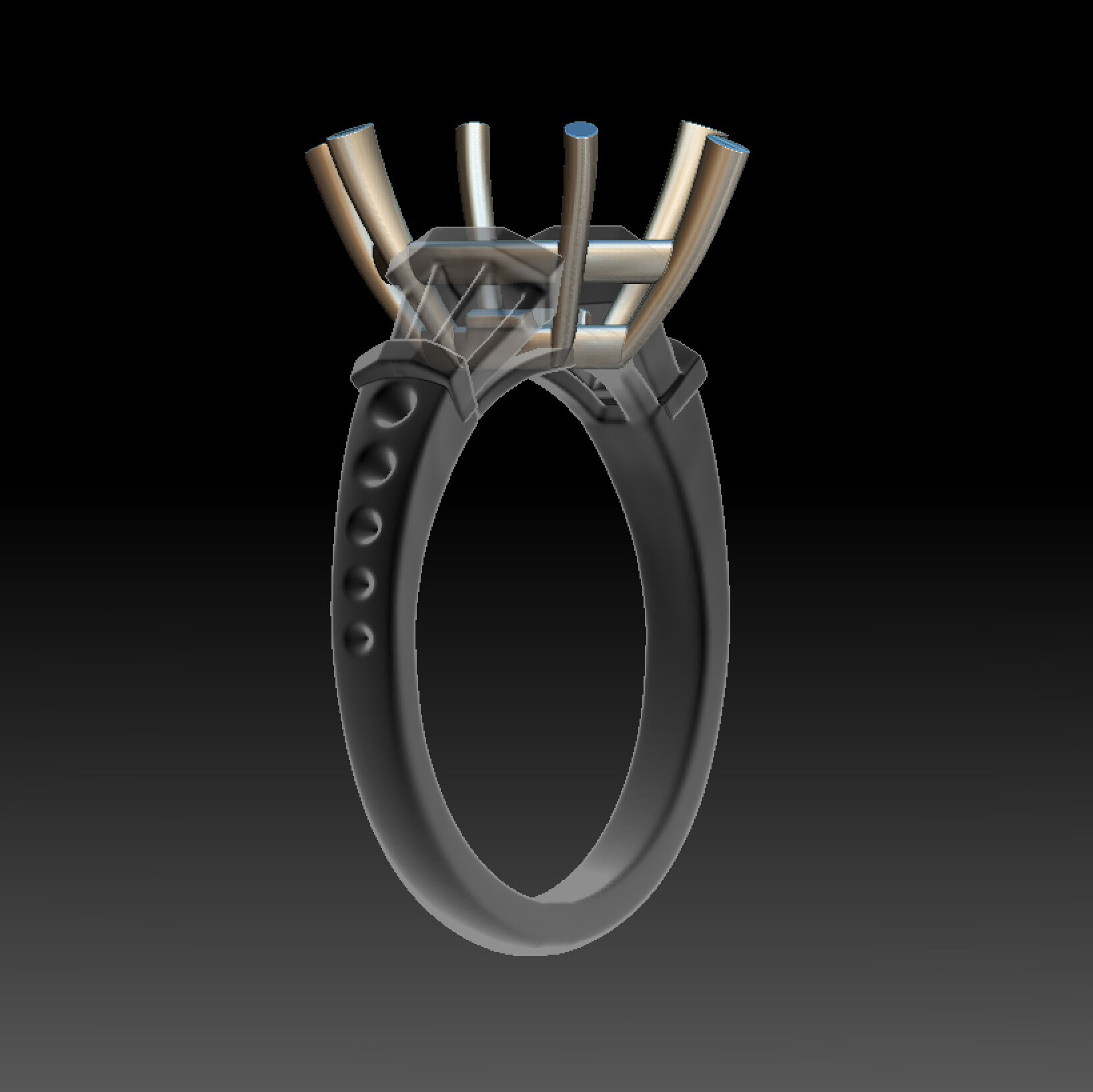
The skilled team at our partner firm used a high resolution multi jet wax printer to create a precise wax pattern of the STL model we had sent them. The wax model was then placed into a flask and a specially formulated powder is mixed with deionised water and a binder solution, which is in turn poured over the flask and model inside, filling it to the top - all under a vacuum to remove bubbles from the mix.
The mixture in the flask is given time to set before being placed in a furnace to burnout the wax model, often overnight, leaving a cavity where the wax previously was. This ‘burnout cycle’ also cures the investment powder to give it maximum refractory properties - ready for casting and the incredibly high temperatures at which platinum is cast at - around 1950ºC to 2050ºC!
The flask is taken from the furnace and placed into the centrifugal casting machine, with the platinum pre-melted and ready to cast into the flask.
Once cast the investment is removed using compressed air and wet-blasting media - stubborn investment is removed using hydrofluoric acid - and you are left with the raw unfinished casting.
The platinum used is from a fully recycled supply chain - refined by one of the largest platinum refiners in the world, based in Pforzheim in Germany - their sources range from industrial, automobile, scientific and electronic waste to old jewellery. This supplier is a member of the Responsible Jewellery Council.
The platinum alloy most used in UK jewellery production using this method is Platinum-Cobalt (950 parts platinum 50 parts cobalt). The cobalt is sourced from Morocco for much of the platinum we use. The cobalt content makes the alloy magnetic!
Once we received the platinum casting back at Timothy Roe HQ, our goldsmiths set to work with carefully filing, emery papering and using rotary tools to pre-polish the ring mount and shoulder collets before the ring was assembled using high grade platinum solders. After this, it was passed on to their colleagues in the setting workshop!
Our stone setting team worked with their tools of choice - the latest GRS and Lindsay Gravers (with palm or foot control) and carried out their painstaking work under a microscope - ensuring the very best level of detail and finish was achieved. We are very lucky to have two stone setters and three goldsmiths on site in our Chichester workshops.
The finished ring set with the client’s 2.33ct - D Colour, Flawless, Marquise Diamond was a true beauty - and one we will be slightly sad to see leave the building! We will look forward to seeing it again in the future for a clean and polish to keep those diamonds sparkling.
A very special thank you to our client for allowing us to include the ring on our website!